Prefabricated bathrooms and kitchens represent a growing trend in offsite construction, with significant applications in commercial and institutional projects. This post examines the market’s current state, focusing on European manufacturers like Baudet and HVA Concept, as well as U.S. companies such as Dorthy Homes. We’ll also examine global leaders in offsite construction, discuss regulatory challenges, and suggest pathways to greater adoption in the U.S.
The bathroom pod is another factory-built component gaining traction in Europe and, to a lesser extent, in North America. This pre-assembled, fully functional unit includes plumbing, fixtures, and sometimes electrical systems, ready for integration into buildings. Ted Benson has used these in his economical homes, but most bathroom pod production is focused on commercial and institutional applications.
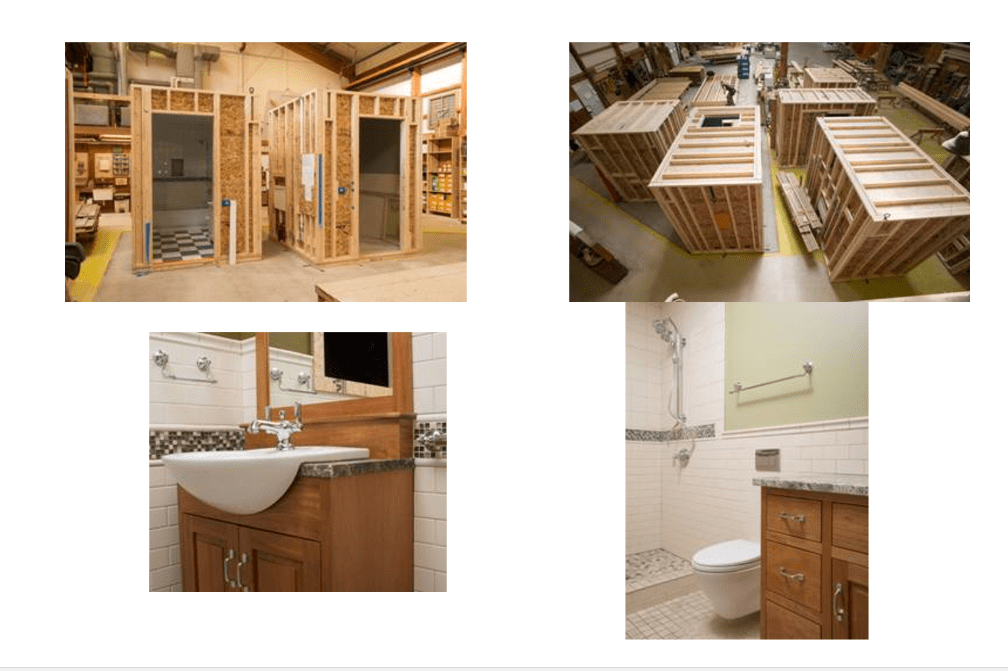
HVA Concept, located in the medieval town of Fresnay-sur-Sarthe, France, manufactures prefabricated bathrooms. They claim to have delivered over 3,000 fully operational units. Combining customization with industrial manufacturing techniques, HVA Concept emphasizes that each ” signed project” is “Designed with a new perspective for 100% personalized results produced in series.” Their bathrooms are adaptable to concrete and wood construction, but their primary market includes institutional and commercial sectors like healthcare, senior housing, collective housing, and the hotel industry.
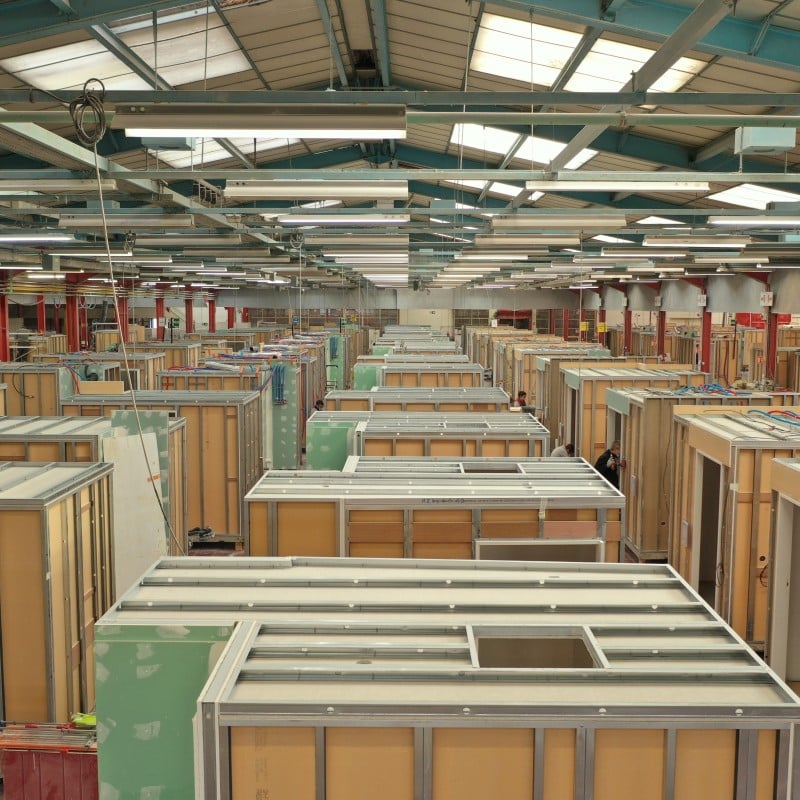
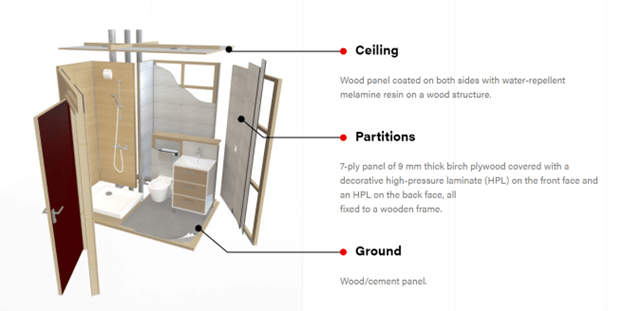
At Batimat, Baudet, a French manufacturer, showcased a line of prefabricated bathroom pods. These units, fabricated from molded polyester rather than traditional wood or steel, offer customizable dimensions within a few inches. Customers can also choose colors and upgrade fixtures. As an added ecological benefit, Baudet highlights that their pods can be moved and refitted for reuse in different buildings. “With lifecycles of over 30 years, Baudet bathrooms can adapt to changing building uses,” the company notes on its website.
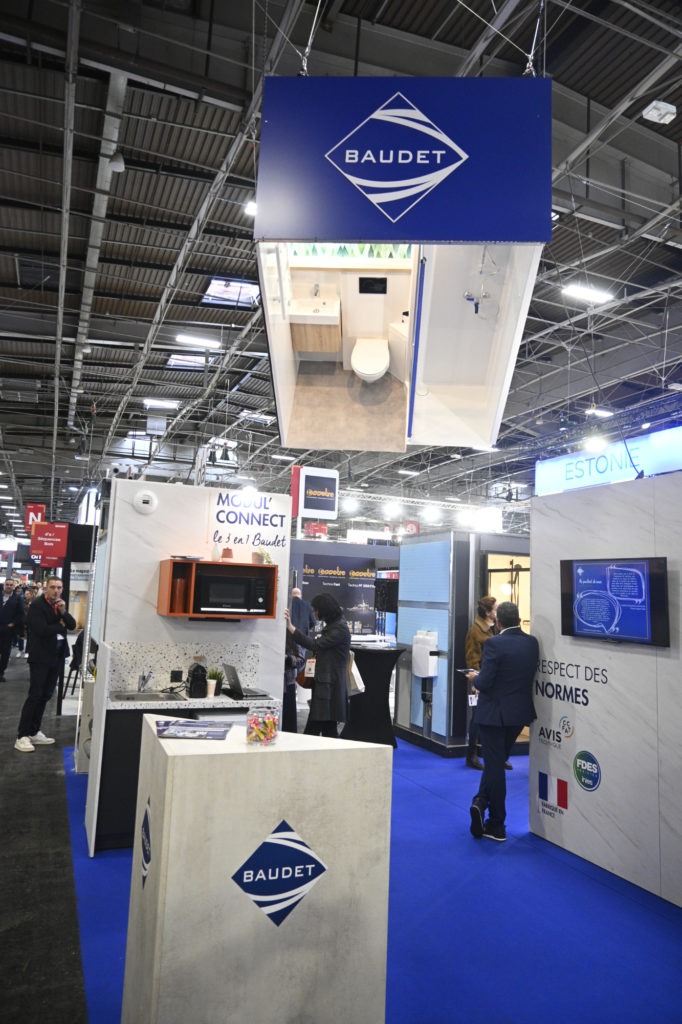
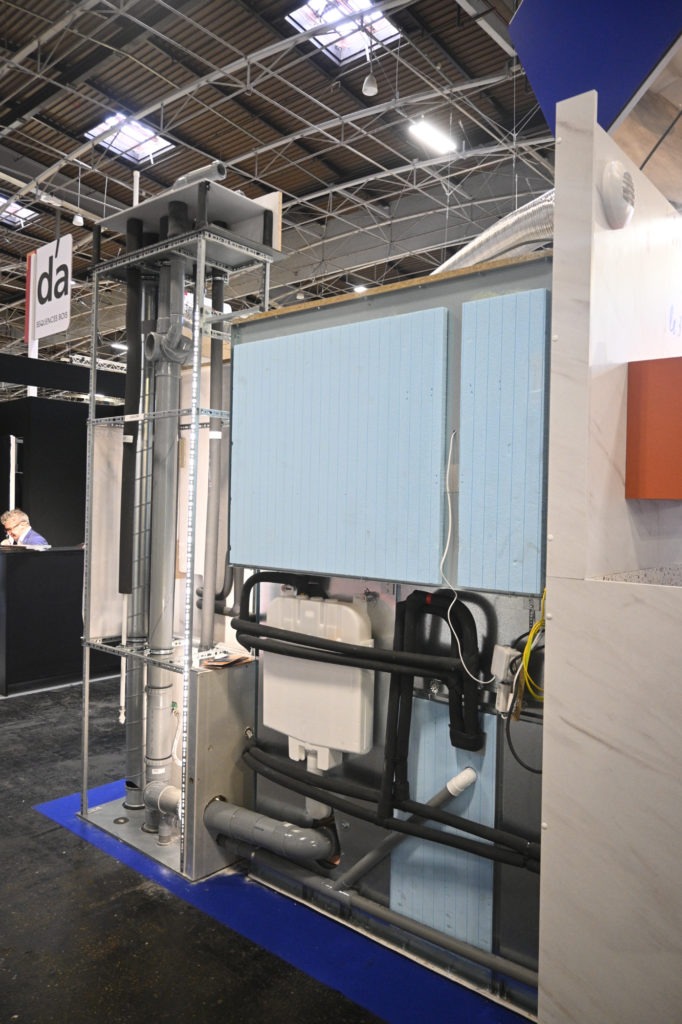
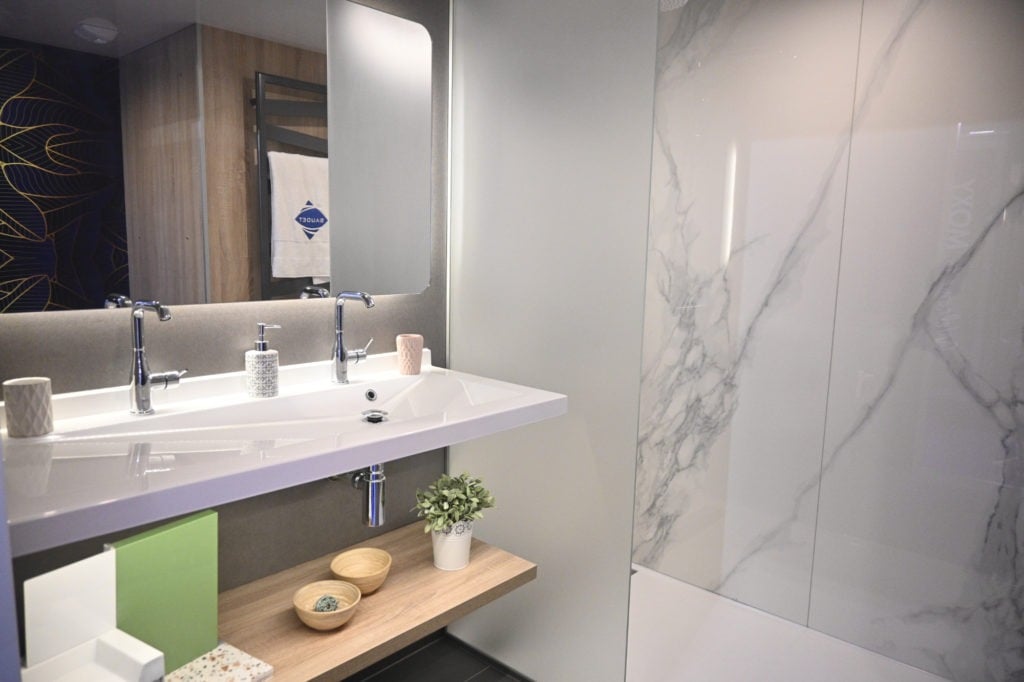
The Unimetal bathroom pods were among the more luxurious bathroom products exhibited at Batimat. Fabricated from cold-pressed, bent steel, these units are lightweight and easy to deliver and install. While they are marketed to hotels, hospitals, prisons, and student housing, the display units at Batimat stood out for their refined, high-end finishes.
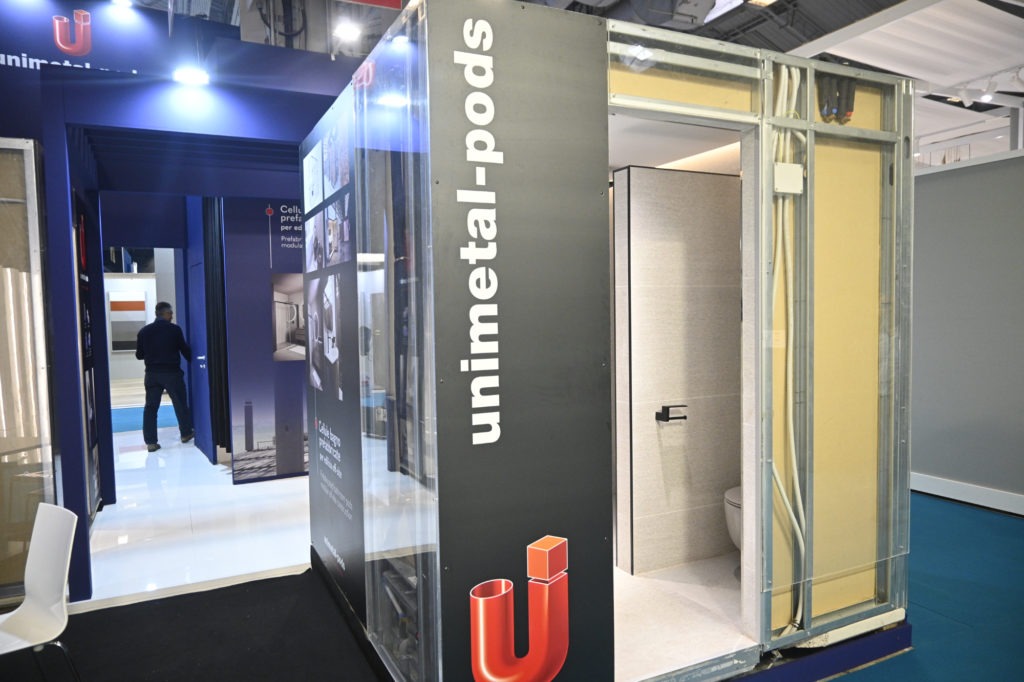
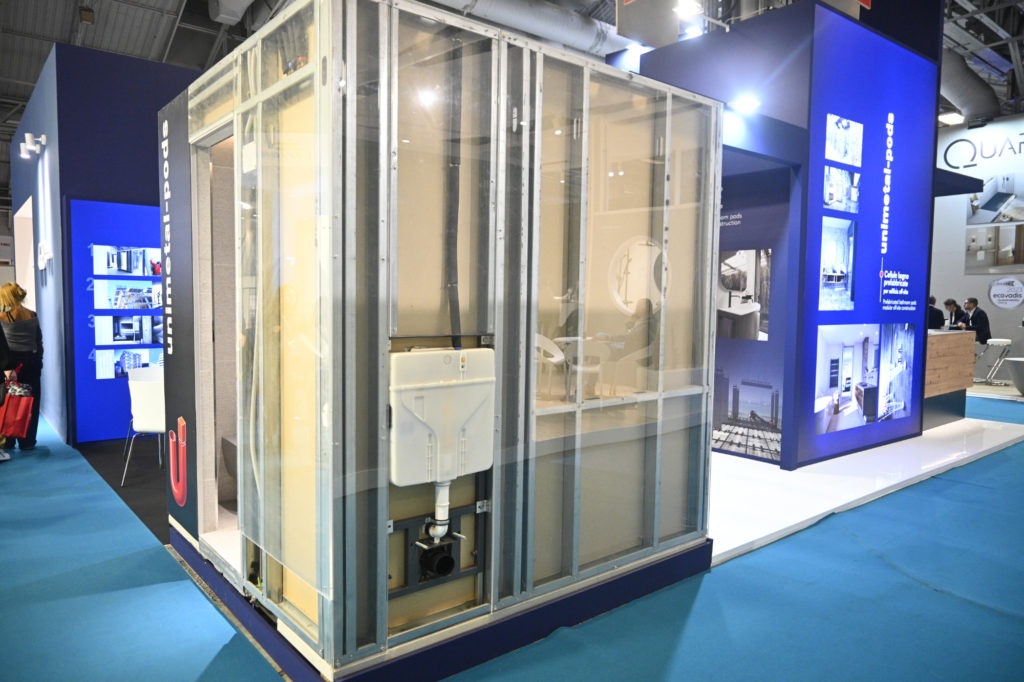
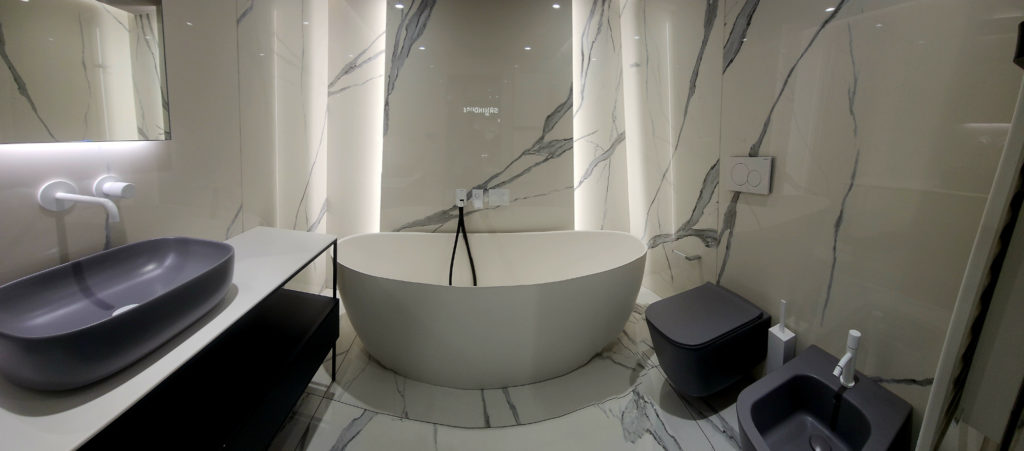
Dorthy Homes showcased prefabricated bathrooms and kitchens at the 2024 International Builders Show, including bathrooms, kitchens, and mechanical-electrical-plumbing (MEP) Pods. Following the event, I visited their Southern California facility to learn more. Stephen Schwartz, an industrial engineer and owner of ATI Windows, has spent the last three years developing prefabricated modules, including handicap-accessible bathrooms, kitchens, and complete MEP walls or closets. Working out of a former lemon-processing plant in Ontario, California, he has experimented with designs that maintain floorplan flexibility while avoiding the transport of oversized modules that require special transport and onsite craning.
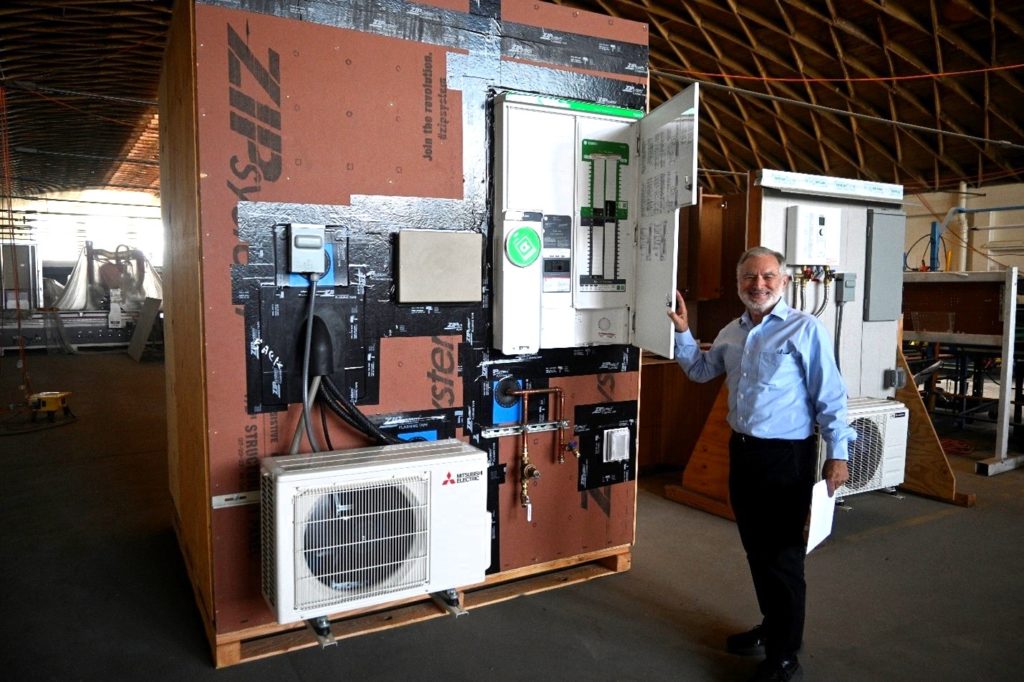
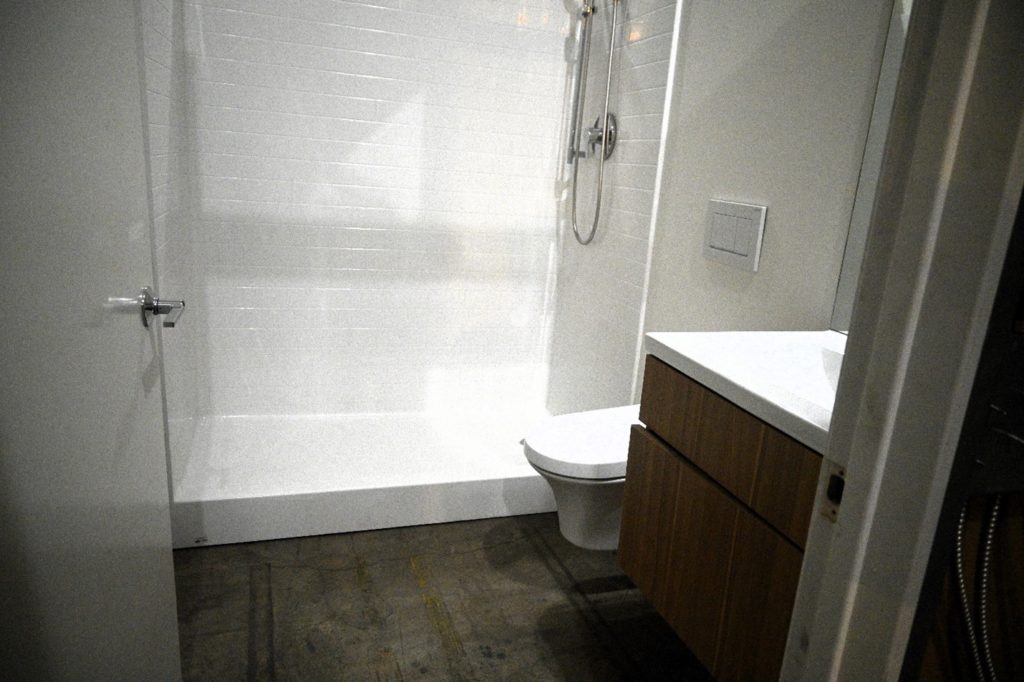
Schwartz’s modules cater to various building types, from garage ADUs to 100-unit apartment buildings. His most popular product is the bathroom pod, which can easily be rolled into place and installed. Delivered on a rolling platform, these pods are unloaded with a small forklift and rolled onto adjustable leveling feet, allowing the bathroom to be set directly onto the floor.
What About Kitchens?
Like bathroom and MEP pods, prefabricated kitchens are gaining interest, although their adoption has been slower due to more significant size requirements and varying design needs.
Dorthy Homes is one of the few fabricators that offers kitchen modules, though Stephen Schwartz admits sales have not met expectations. At Batimat, I found only one kitchen vendor, with products primarily suited for small apartments and student housing.
While companies like Dorthy Homes are experimenting with prefabricated modules in the U.S., the European market has already embraced similar solutions, particularly in small apartment and student housing units.
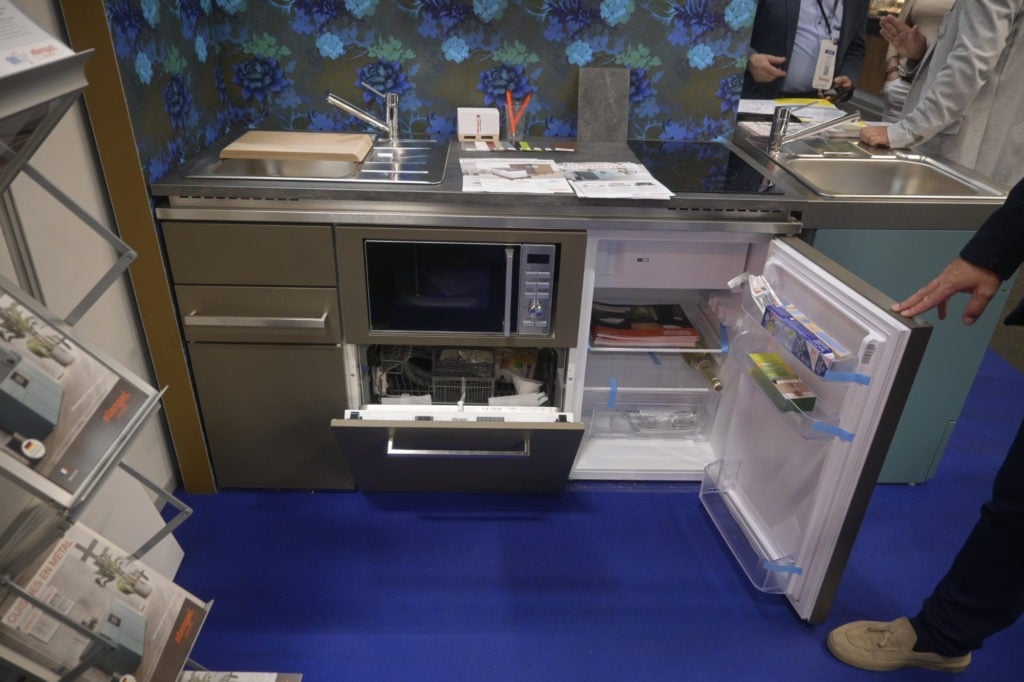
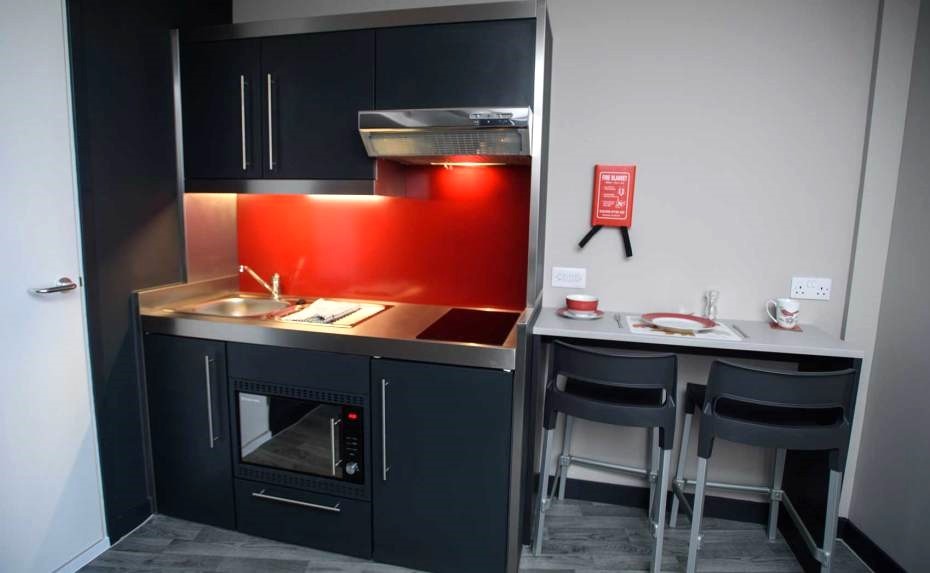
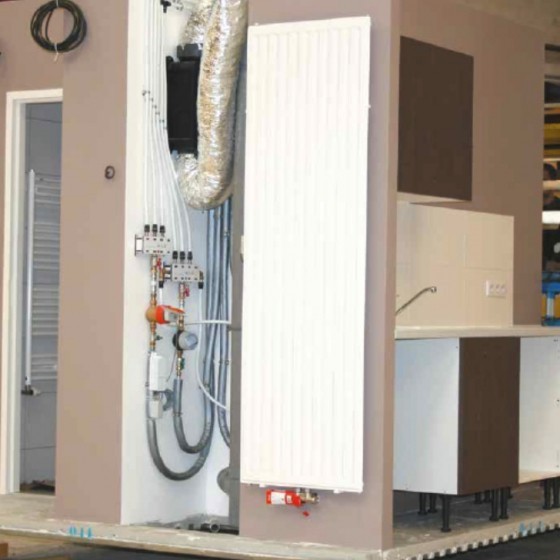
The challenge with prefabricated bathrooms and kitchens lies in their size and the wide range of layout and style options, making them less adaptable to a standardized, pod-like configuration for residential use. Kitchens are often large and not arranged in a single line, unlike bathrooms, which can be more easily standardized for broader applications. Given the high costs of transportation and craning pods into place, manufacturers have found more success with smaller modular units that offer greater flexibility for a variety of floorplans.
The increasing adoption of prefabricated bathroom and kitchen modules reflects the offsite construction industry’s push toward more efficient, streamlined building practices. While significant progress has been made, particularly in Europe, challenges remain, including the variability of demand and the need for flexible designs that accommodate diverse architectural requirements. Addressing these hurdles will be crucial for broader adoption as the industry continues to evolve. In the next post, we’ll explore the key challenges facing the offsite construction industry, from regulatory barriers to market dynamics, and examine potential strategies for overcoming them.