As modular construction evolves, panelized facades can significantly advance offsite building practices, particularly in retrofit applications aimed at improving energy efficiency and reducing timelines. While Europe leads in adopting complete wall systems with pre-installed elements such as windows and cladding, North America is gradually catching up by exploring mass timber framing and other innovations. This section delves into the latest advancements, benefits, and challenges of panelized construction, starting with insights from Batimat and highlighting the approaches taken by companies pioneering this field.
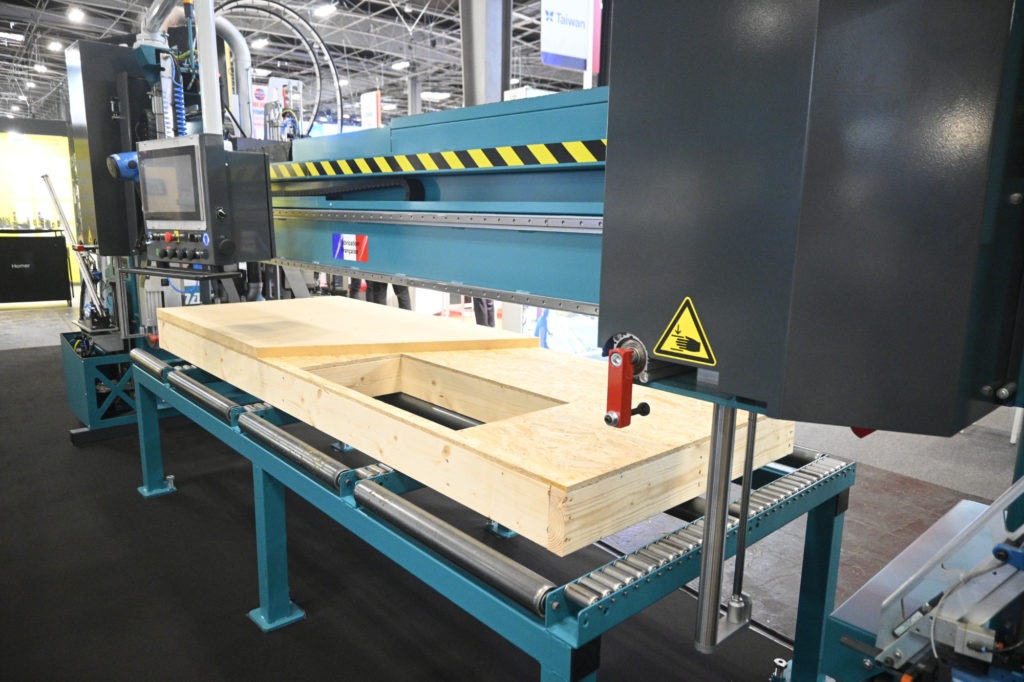
In the United States, panelized construction—where large wall or floor sections are built in a factory and transported for on-site assembly—is limited primarily to factory-framed walls and floor cassettes with studs, joists, and sheathing. Unlike Europe, where the industry has advanced to include more complex methods, it’s rare in North America to find manufacturers delivering exterior walls with windows and siding pre-installed. One exception is ACQBuilt, an Alberta-based company, though this approach remains uncommon in North America, while it’s standard practice in much of Europe.
The UK is shifting rapidly toward off-site construction, with nearly 15 percent of new buildings originating in factories. In London, cast-in-place facades have given way to prefabricated structural systems, where columns, beams, and slabs are combined with pre-made facades and even bathrooms craned into place later.
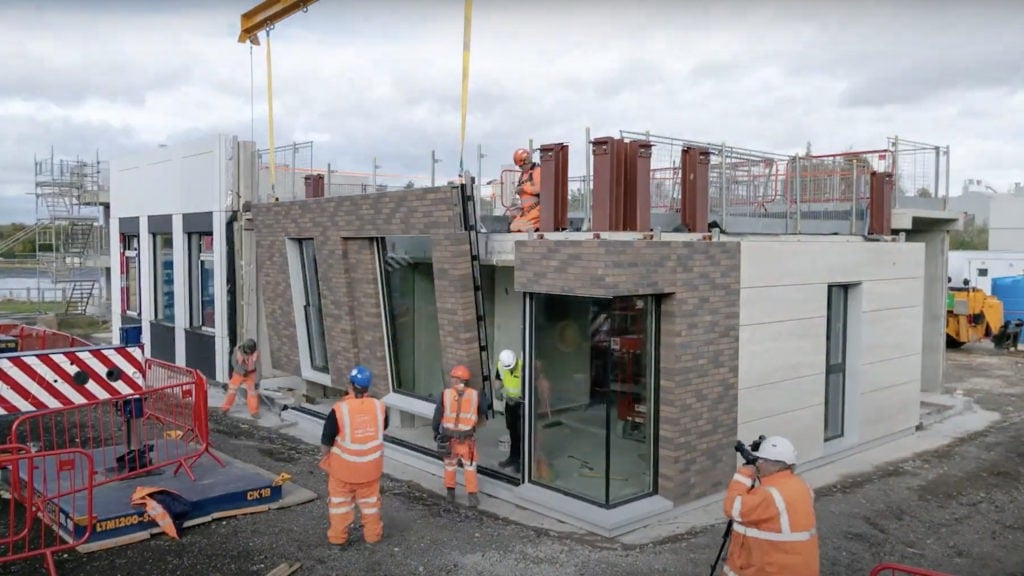
While panelized construction has matured in Europe with advanced methods like pre-installed windows and finished, thoroughly insulted facades that can be applied over existing buildings, the U.S. industry remains focused on basic structural components. In North America, panelized construction is confined mainly to framing systems, though some companies are starting to adopt more complete solutions.
One unique area of European application of prefabricated components is retrofitting older buildings with high-efficiency facades. According to Martin, the Dutch Energiesprong initiative plans to retrofit 800,000 apartments using prefabricated packages for facades and roofs. This approach shortens timelines from weeks to months by mass-customizing components to fit existing buildings.
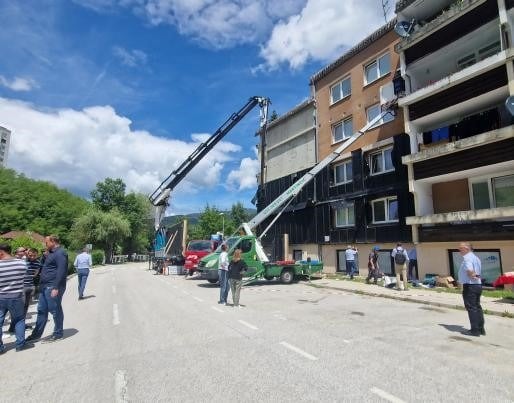
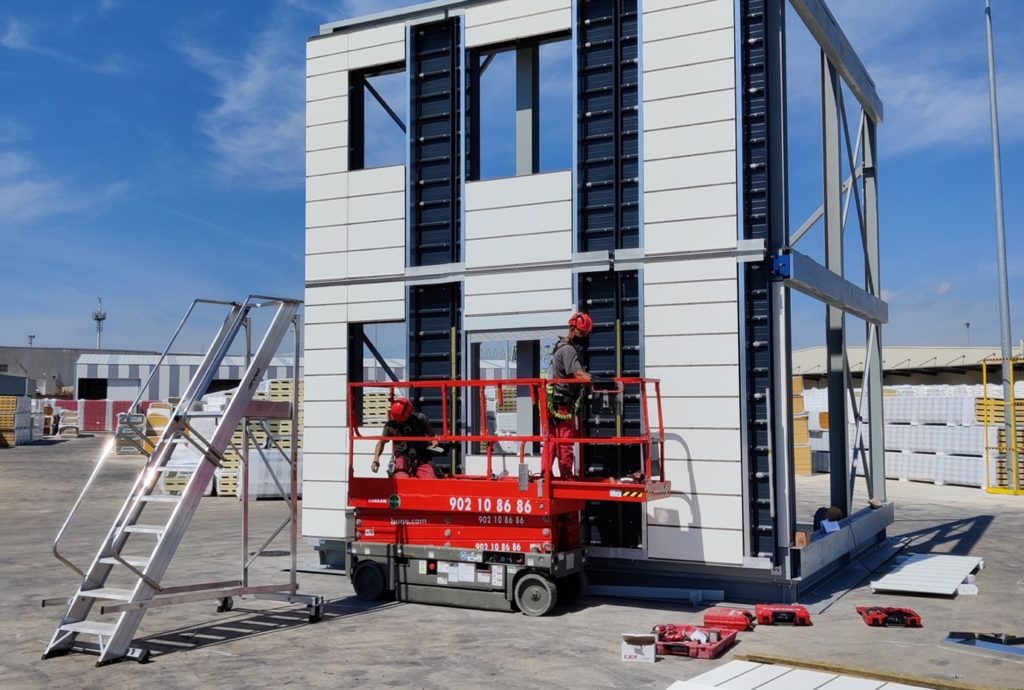